InnoTech Alberta partners with industry and manufacturing to develop higher-value bio-composite materials through a combination of scrupulous scientific research, testing, and overall process validation. The applications for our expertise and facilities are wide and varied. We can partner with clients from the forestry and pulp industry, to agriculture, to homebuilding and furniture to produce new bio-composite material or improve existing ones.
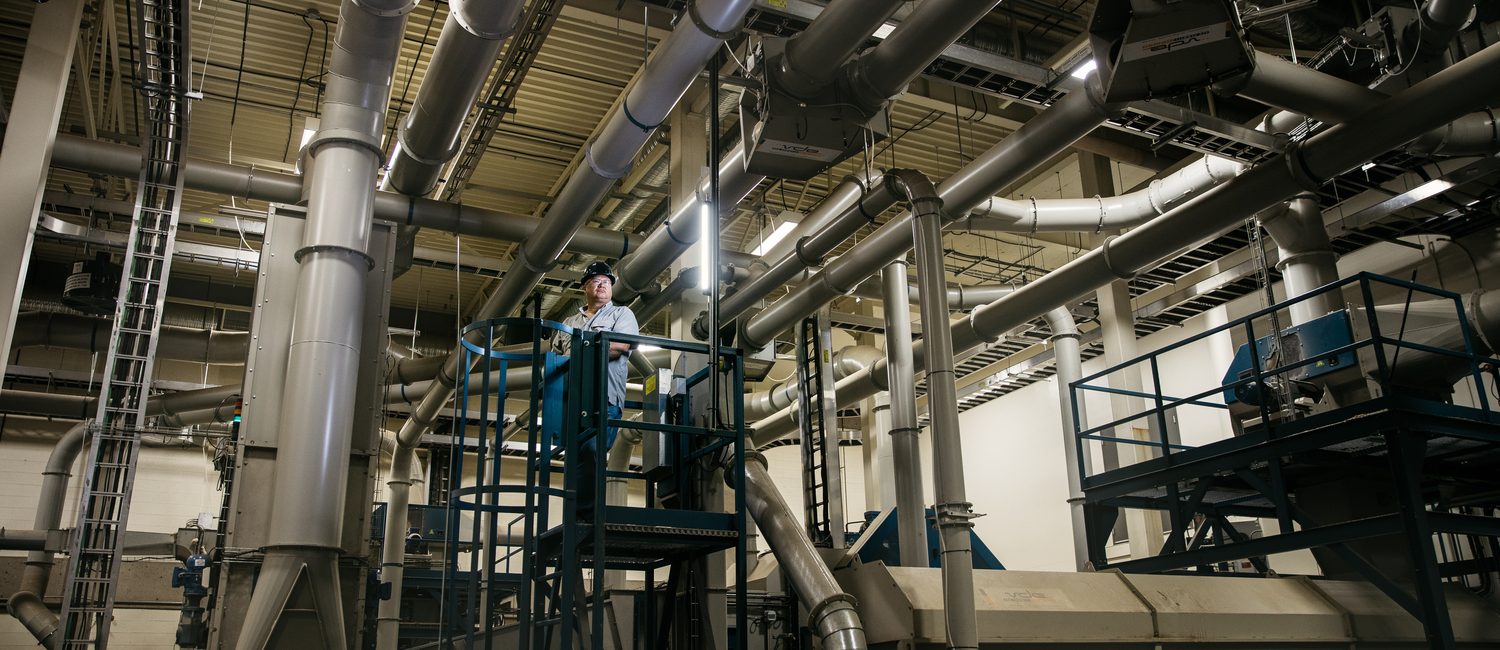