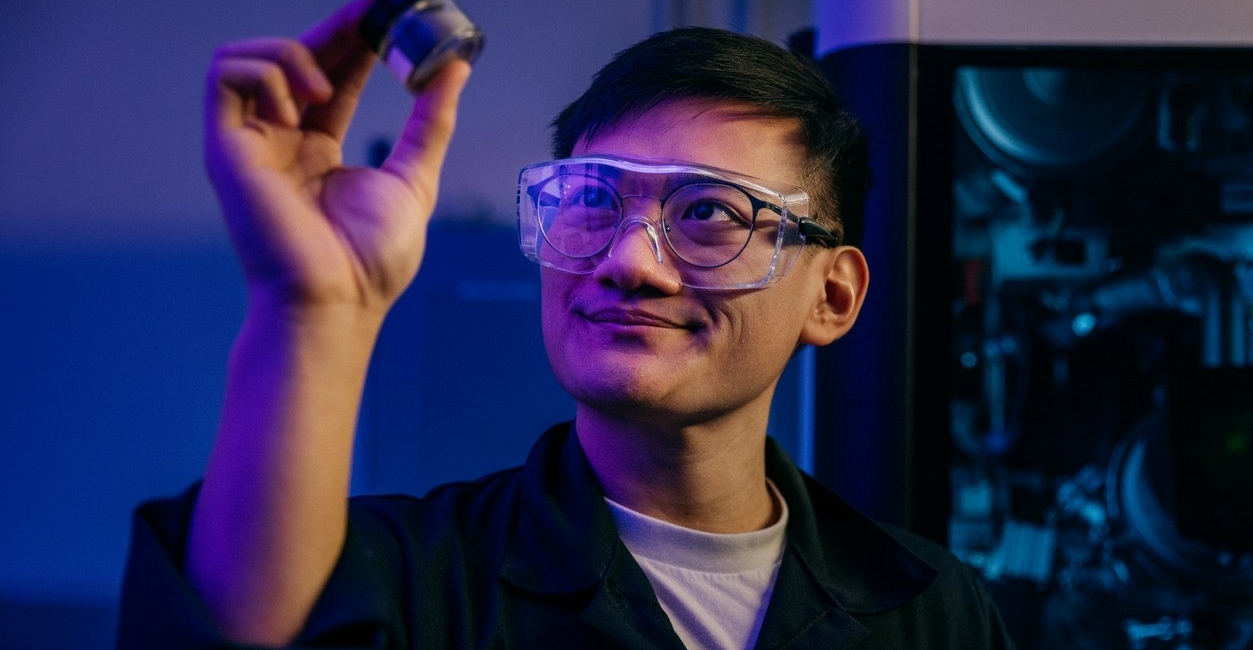
When Dr. Dave Waldbillig of InnoTech Alberta looks over his desk, he sees all the usual knickknacks—stationary, souvenirs, and company swag—with a twist: he 3D-printed much of it himself, using metal powder processed in InnoTech’s Ultrasonic Powder Atomizer.
To do so, Dr. Waldbillig feeds solid metal into the atomizer, melting it down with a powerful electric arc. Once the metal is molten, an ultrasonic frequency breaks down the molten pool into tiny spherical droplets that solidify into a fine powder. This powder can become whatever he wants using a laser powder bed metal 3D printer. The products of this remarkable process are all over Dr. Waldbillig’s desk; ask and he’ll happily show you miniature InnoTech and Alberta Innovates logos printed from stainless steel powder.
Professionals like Dr. Waldbillig use the InnoTech atomizer for much more than logos. InnoTech’s machine is a unique small-scale unit, about the size of a fridge, designed for cutting-edge research and development in additive manufacturing (3D printing). By adjusting variables such as arc current and ultrasonic frequency, he can use the InnoTech atomizer to accommodate many different conventional input metals, to make larger or smaller particles, and to make entirely new materials like wear resistant composites and high entropy alloys.
While there are some industrial-scale atomizers in Canada, InnoTech’s atomizer is the only one in the country that is designed to create small batches of customized and novel powders from metals old, new, and yet-to-be-invented. InnoTech is currently working with a wide variety of universities, government agencies, and industry players who want to make full use of the atomizer’s vast potential.
No need to worry about missing out if you’re not an active technoscience researcher or industrial engineer: we’re all getting the benefits that atomizers and 3D printers bring to the economy and environment. Additive manufacturing has next to no material waste, because when an object completes the printing process, excess powder is vacuumed up for reuse in a new project. What’s more, scrap metals can be melted down and atomized into new powder, reducing waste from more traditional modes of manufacturing as well.
InnoTech is already using its atomizer and metal 3D printer to produce parts for internal InnoTech projects and startup companies, and specialized components locally for Alberta’s energy and other industries. With heat, inert gas, and some good ultrasonic vibrations, the atomizer and metal 3D printer are removing excess costs and CO2 in what may be their greatest creation of all: a green circular economy.
And who knows? Someday, we may be able to print our own gifts, sculptures, tools, or whatever else we can dream up, making them from materials that flew straight out of Star Trek and into our reality.