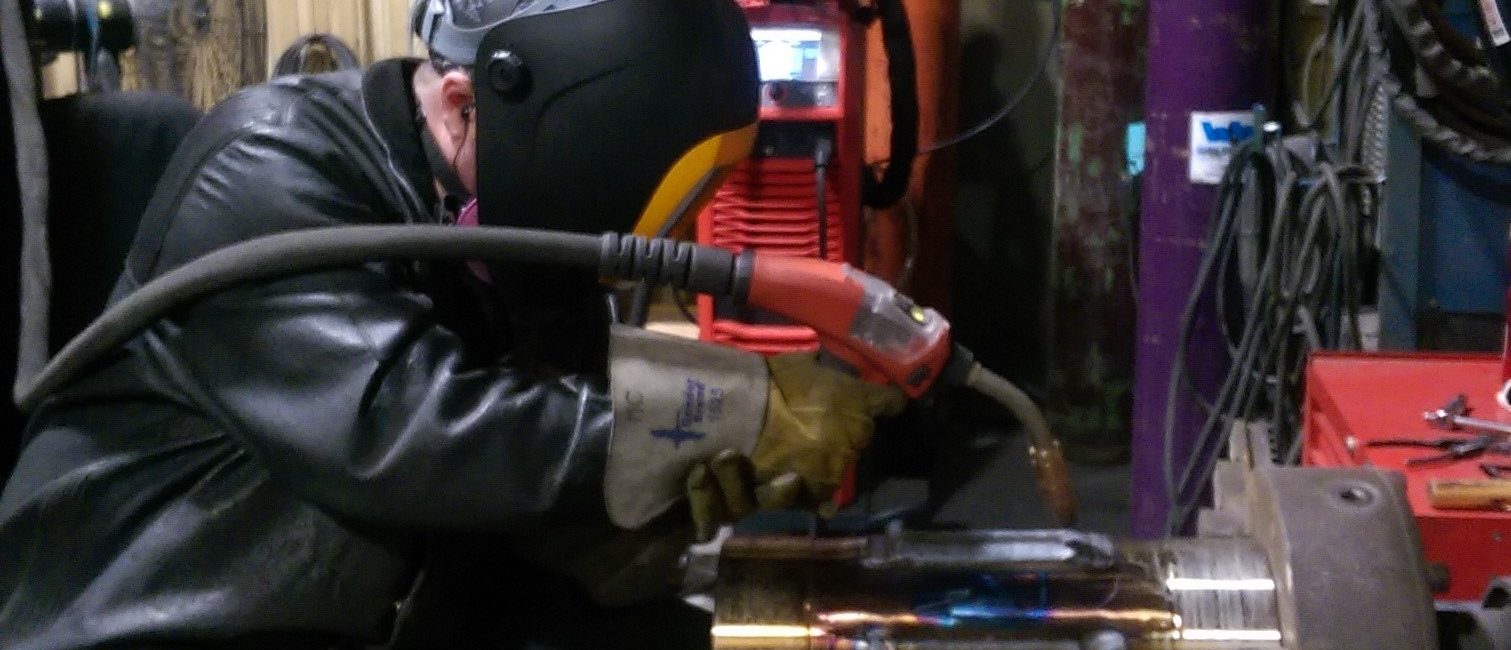
As welding staff in Northern Oil Tool increasingly struggled to keep up with customer orders, Norm Briggs, the company’s quality manager, recognized a possible bottleneck and began to search for answers.
Briggs identified that the company’s older stick welding equipment needed replacing, and that a cold metal transfer (CMT) system — a new form of welding that uses extremely low heat and an exceptionally stable arc to weld different materials efficiently — was an ideal solution.
InnoTech Alberta’s Alberta Manufacturing and Fabrication Innovation (AMFI) Program offered the technical expertise and advice required to implement the new system. An equipment demonstration arranged by AMFI and vendor Fronius Canada, showed CMT could cut welding time from 6.5 hours to just an hour and 45 minutes to produce the same part.
“We have very high demand for parts but we just couldn’t keep up with demand,” says Briggs, who oversees quality control at the 21,000-square-foot facility in Leduc, Alberta. Here, about 40 welders, machinists and operators produce components, such as drive shafts and drilling tools, for the oil and gas industry.
First, Briggs sat down with welding staff in the company’s boardroom and together they began to pour over every detail of the plant’s welding processes, floor layout and equipment. Later, prompted by their discussion, he began to research options to replace the company’s older stick welding equipment. As he read more, he focused on a cold metal transfer (CMT) system.
Then, realizing he needed technical help, he turned to the Alberta Manufacturing and Fabrication Innovation (AMFI) Program. Offered through InnoTech Alberta and funded by the Alberta Ministry of Economic Development and Trade Industrial Growth Solutions and the National Research Council’s Industrial Research Assistance Program, AMFI works with manufacturers to accelerate the adoption of advanced technologies. InnoTech Alberta provides technical expertise and research facilities, and is a wholly owned subsidiary of Alberta Innovates.
“As I started to talk to the people at AMFI, I found out that they were very familiar with CMT and they were very supportive. They helped us build a relationship with the equipment vendor. They also recommended the right equipment model for our work,” Briggs says.
Next, Northern Oil Tool and AMFI teamed up with a vendor, Fronius Canada, specializing in CMT welding systems, and together they arranged an equipment demonstration at Northern Oil Tool’s plant. As Briggs and his team evaluated the equipment, AMFI’s team provided guidance.
“We’re not a big shop at Northern Oil Tool. So AMFI provided critical technical input for us and were involved in all the discussions,” Briggs says.
The equipment trial, performed by Mike Pioker, one of Northern Oil Tool’s welders, proved highly promising, showing CMT could cut welding time from 6.5 hours to just an hour and 45 minutes to produce the same part. With these results, the company decided to go ahead and purchase the CMT system.
Since then, the investment has paid off. Since early August, welders in the plant have used the new welding equipment to apply buffer (base) layers, the first application in its welding process. In the first month of use, Briggs says, the company saved more than 200 hours of labour and reduced the costs of welding consumables including shielding gas by 62 per cent. With these savings, the return on investment (ROI) on equipment was achieved in less than a month.
With this success, the relationship between Northern Oil Tool and AMFI continues to grow, as the company explores new applications for its CMT equipment. Right now, the company is working with AMFI and the surface engineering team at InnoTech Alberta to test the equipment’s ability to apply hard facing coatings to protect metal parts.
“We’re already ahead of the game with CMT. But if we can adopt the technology for other applications, we could increase our productivity even further.”